2002-ին մեր ընկերությունից ստացվող երկու ձեռնարկություն արտադրող ձեռնարկություն ձեռք է բերել մեր ընկերությունից երկու ձուլման կամուրջի ամբարձիչներ, ձուլման արհեստանոցում հալած չուգուն նյութերի տեղափոխման համար: Ductile Iron- ը չուգունի նյութ է `պողպատին համարժեք հատկություններով: Ձեռնարկությունն օգտագործում է այս նյութը `շինարարական եւ գյուղատնտեսական տեխնիկայի արտադրության արդյունաբերություններում օգտագործման համար բարձր ամրության մասեր արտադրելու համար: Այս երկու ամբարձիչները դեռ կարող են օգտագործվել սովորաբար 16 տարվա օգտագործման ընթացքում: Բայց պրոֆեսիոնալ ձուլման տեխնոլոգիայի պահանջարկի շարունակական աճով, երկաթե սանդուղքը, որը պետք է տեղափոխվի, կարող է բեռնել մինչեւ 3 տոննա հալած նյութ, գերազանցելով առկա ամբարձիչների բեռի հզորությունը: Օգտագործողը քաջատեղյակ է այս տեսակի գործընթացի համար կռունկների ձեւավորման համար Սեւեննինի լայն փորձի մասին, եւ հետեւաբար կրկին մեզ մոտեցավ: Մենք փոխարինեցինք ձուլման աշխատաժողովում 50.5 մետր երկարությամբ կռունկով հետընթացը եւ տեղադրեցինք երկու նորՁուլման կամուրջի ամբարձիչներ, բարձրացնելով գնահատված բեռի հզորությունը 10 տոննա:
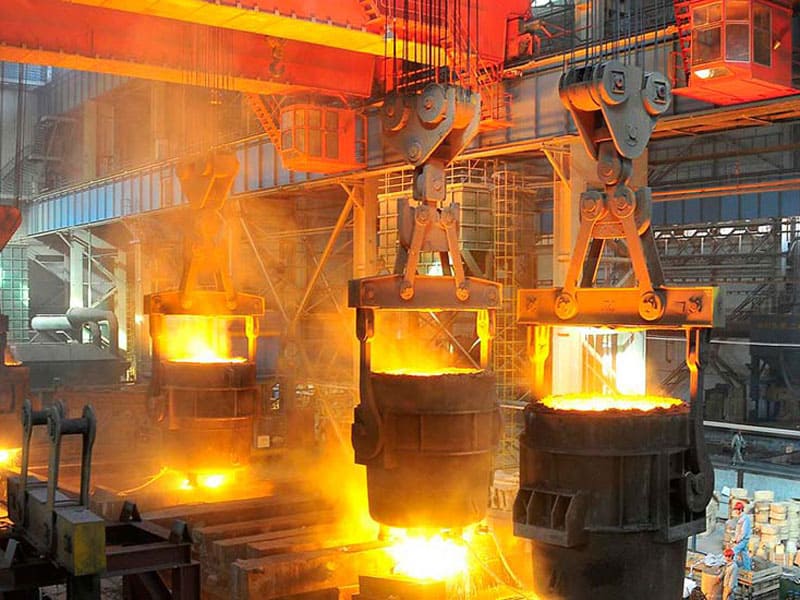
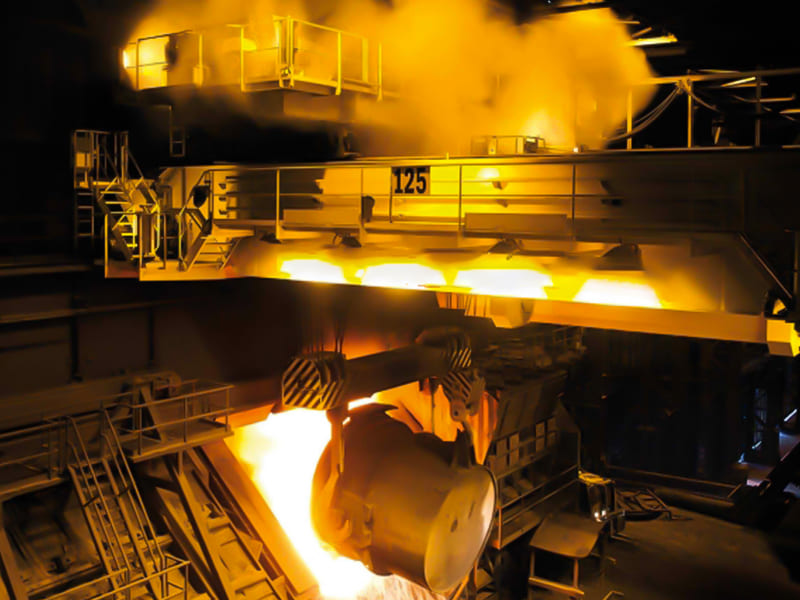
Այս երկու բոլորովին նորՁուլման ամբարձիչներՀանդիպեք EN 14492-2 ստանդարտով սահմանված հատուկ պահանջներին `շրջակա միջավայրի ծայրահեղ պայմաններում վարագույրների բնականոն աշխատանքը ապահովելու համար: Նոր ձուլման կռունկը դեռեւս օգտագործվում է իր ձուլման արհեստանոցում `հալած երկաթե փաթեթներ տեղափոխելու համար 1500 ° C ջերմաստիճանով ջերմաստիճանի միջոցով: Կռունկը այն փոխանցում է հալվող վառարանից դեպի թափվող բեռնատարը: Այնտեղ, բարձրորակ ճկուն երկաթե նյութը լցվում է բորբոս եւ դատարկության գործընթացում ավարտելուց հետո դատարկումը: Այս երկու ձուլման արհեստանոցներում կամուրջի ամբարձիչները հիմնված են հասուն ունիվերսալ կռունկների տեխնոլոգիայի վրա եւ նախագծված ոչ ստանդարտ, լիովին բավարարելով օգտագործողի ձուլման արտադրամասի խիստ պահանջները:
Սեւեննանը սերտորեն համագործակցեց օգտագործողի հետ եւ գործարանի հանգստի ժամանակահատվածում ապամոնտաժեց հին կռունկը: Դրանից հետո տեղադրվել են նոր կռունկներ եւ կռունկներ, իսկ էլեկտրամատակարարումը նույնպես թարմացվել է եւ կառուցվածքային փոփոխության մեջ: Միեւնույն ժամանակ, թափելու մեթոդը կթարմացվի ձեռքով թափելով էլեկտրական լցնելով ձեռքով: Օգտագործողի հակիրճ արձակուրդից հետո նրանց ձուլման աշխատասենյակում աշխատողները այժմ կարող են աշխատել նոր կռունկ: Այս նոր ձուլման ամբարձիչները օգտագործում են ամուր կռունկային բաղադրիչներ, որոնք սկզբից կարող են սահուն վազել: Մենք մեկ անգամ եւս ցուցադրել ենք օգտագործողին կոշտ պայմաններում մեր կռունկների հուսալիությունը, անվտանգությունը եւ արդյունավետությունը:
Փոստի ժամանակը, Մայիս -08-2024